How to retrofit underfloor heating – a complete guide
We explain everything you need to know about installing UFH in an existing home
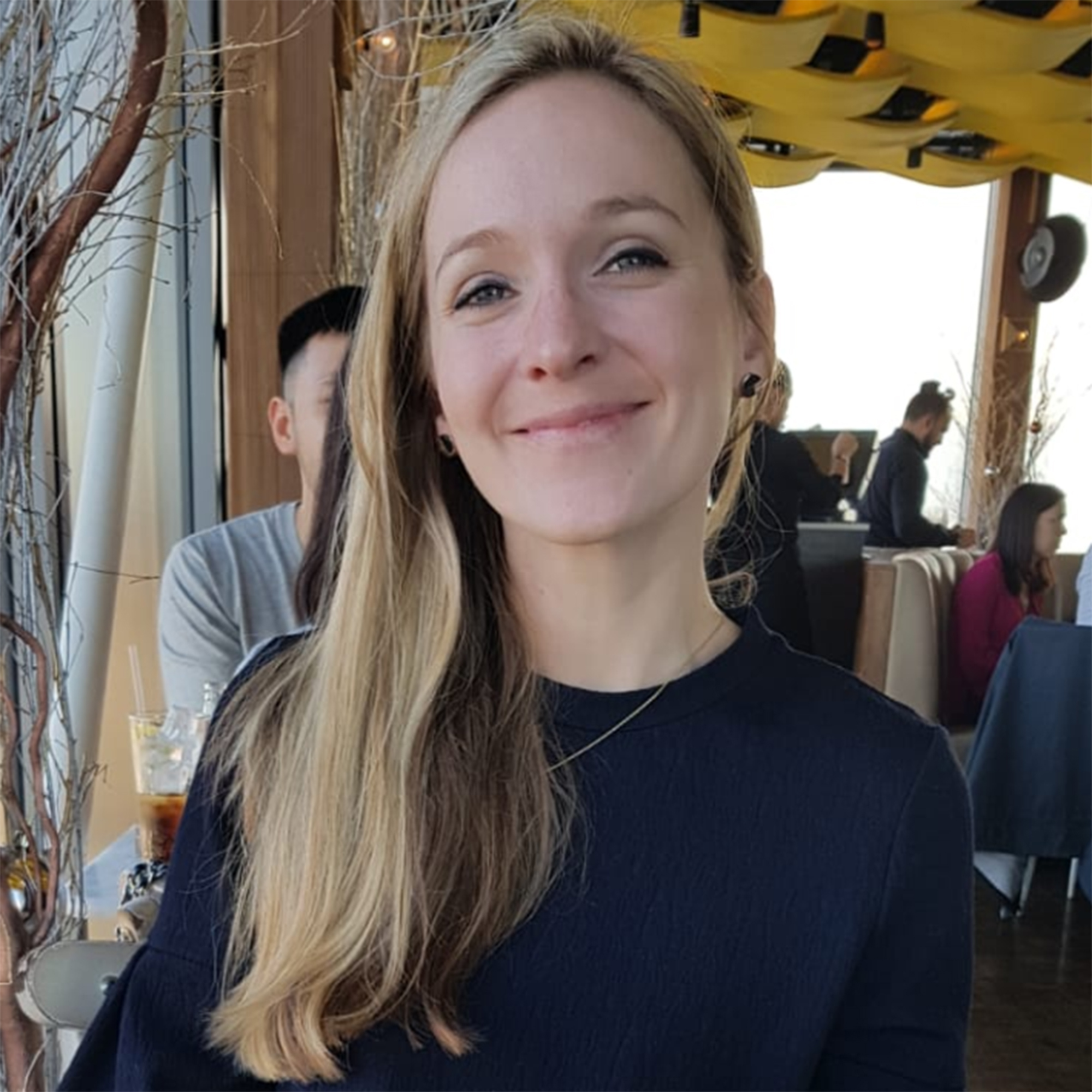
Underfloor heating (UFH) is a popular choice for heating home, so it's no surprise that people are asking how to retrofit underfloor heating. While installing underfloor heating in an existing home as part of a renovation doesn’t offer quite the same clean slate for installation as a self-build would.
That said, this still doesn’t mean underfloor heating is out of the question. There’s a selection of specially designed systems tailored towards renovation projects. It’s simply a case of tracking down the product that best suits your house’s characteristics.
How to retrofit underfloor heating – the step-by-step process
Thanks to a thin height build up and easy installation, electric systems were once the go-to solution for retrofit scenarios. However, thanks to the development of many slim, low-profile systems, how to retrofit underfloor heating in an existing house is more achievable than ever.
'It’s particularly reassuring to know that you no longer need to dig up your floors to bury a system beneath six inches of screed and cement,' says Tom Edmunds, general manager at Wunda Group.
1. Decide on the most appropriate system to retrofit
When it comes to how to retrofit underfloor heating, you need to begin by choosing the correct setup, and there are several key factors to bear in mind here. The first is the thermal efficiency of your home. If the house is poorly insulated with single glazed windows, the thermal fabric will likely require upgrading to ensure UFH can run efficiently. The type of subfloor you have also plays a big part in the decision, too. As will the amount of upheaval required for installation.
Underfloor heating to an existing space can be divided into two categories. Systems that warm the floor surface via electrically heated cables, or those that comprise a network of pipes filled with warm water. The one you choose will depend on how many rooms you’re fitting UFH in. Plus how much you want to spend on installation and how much you’re willing to spend on running costs long term.
- Electric underfloor heating comes either in loose cable form or with the wires embedded into a sticky mat. It’s easy to lay directly atop the subfloor and have little impact on floor heights – a key factor for many renovations where you can’t change ceiling heights and door levels. Many of these, such as the electric underfloor heating from The Underfloor Heating Store, will feature an extremely thin heating wire which can be installed directly in a layer of tile adhesive when you’re fitting the system alongside a tiled surface.
- Warm water screeded. In this system, warm water pipes are embedded into a layer of sand and cement screed that helps spread the heat across the floor surface. In the past, the height build-up from this layer would have required the removal of skirting boards and for the bottoms of doors to be trimmed down to fit. However, modern low-profile systems for renovations are designed with a thin, self-levelling liquid compound in place of the screed. This can reduce the typical height of the system from around 75mm to as little as 15mm, depending on the product you go for.
- Warm water non-screeded. Hydronic systems with no screed can also be known as ‘dry’ – don’t confuse them with electric UFH, which is sometimes described using the same terminology. Here, pre-routed tubes are laid into a panel, which often features a layer of foil on top to help spread the heat effectively. Overlay systems like this can be laid directly onto the existing floor and are ideal for homes that don’t have the vertical space for a screed or self-levelling compound.
2. Budget correctly
Before you start your project, bear in the underfloor heating costs. If you’re working with how to retrofit underfloor heating, bear in mind that any renovation project comes with more unknowns than if you were working with a brand-new building. That’s why it’s so important to build a contingency fund into your overall budget.
It’s generally acknowledged that laying UFH in an existing home will be more expensive than in a fresh new self-build, too – especially if you’re making thermal upgrades to your house as part of the process.
Electric underfloor heating costs less to install than warm-water systems as it’s so easy to fit. However, it will result in higher running costs later.
If you’re only fitting it in the family bathroom and an ensuite, that may not be a problem. However, if you’re retrofitting UFH across the entire ground floor, a hydronic system will probably be more cost-effective in the long-term.
3. Inspect your subfloor
If you have suspended timber floors (eg a period property), there are two options. One is to take up the floorboards completely and lay the underfloor heating pipes so they’re suspended between the joists, with a layer of insulation underneath. A sand and cement mix would then be poured around the pipes on top of the joists. If adding the screed layer is going to cause any issues, a low-profile overlay system with insulated backing boards might be the better option, as it can be laid on top of existing floorboards.
For how to retrofit underfloor heating in home with concrete slab floors, the process will generally be less labour intensive as you can simply lay UFH over the top of the floor slab. A screeded solution will offer the best heat output, however, if you don’t have the vertical height to accommodate that, a modern slimline product might be the best match.
Electric systems can typically be laid over concrete slab and suspended timber floors without any difficulties.
4. Lay a suitable flooring on top
Many materials are compatible with underfloor heating, but if you want your floor to conduct the heat effectively into the room above, dense tile surfaces have the edge. Solutions such as porcelain and ceramic are smooth and level, so you’ll get an even spread of warmth across the whole tile. Stone works well, too.
Timber is a possibility, though it won’t match porcelain or ceramic tiles in terms of its heat conductivity. Engineered products made from several cross-laminated layers of plywood, finished with a top veneer, are typically chosen over solid boards. Any floor finish that uses solid wood will need to be designed properly to allow for expansion and contraction as the wood heats and cools with your heating.
If you’re after a soft feel underfoot, you can have underfloor heating with carpet. However you’ll need to ensure the combined value of the carpet and the underlay doesn’t exceed the Tog value specified by your UFH supplier. Otherwise, the layer of carpet will be too insulating for heat to move up into the room above.
Are there any other key considerations?
As it’s a low-temperature heat distribution system, UFH works best in homes that don’t leak heat through the walls, floors and roof. 'To prevent heat loss, it’s always a plus to add insulation or improve the quality of the windows and doors as much as possible,' says Michael Schienke, director at Vorbild Architecture. 'Some of this may require separate permissions, but it’s always a plus to upgrade old single glazed windows to double glazed.'
When it comes to how to retrofit underfloor heating, floor profile is another key factor. 'One of the biggest issues we face is keeping the existing floor finish level if you have areas in the house with UFH and areas without it positioned side by side,' adds Michael. Getting this aspect of your project right will come down to careful planning at the design stage. And making sure you choose the right product in terms of height build-up.
Get the Ideal Home Newsletter
Sign up to our newsletter for style and decor inspiration, house makeovers, project advice and more.
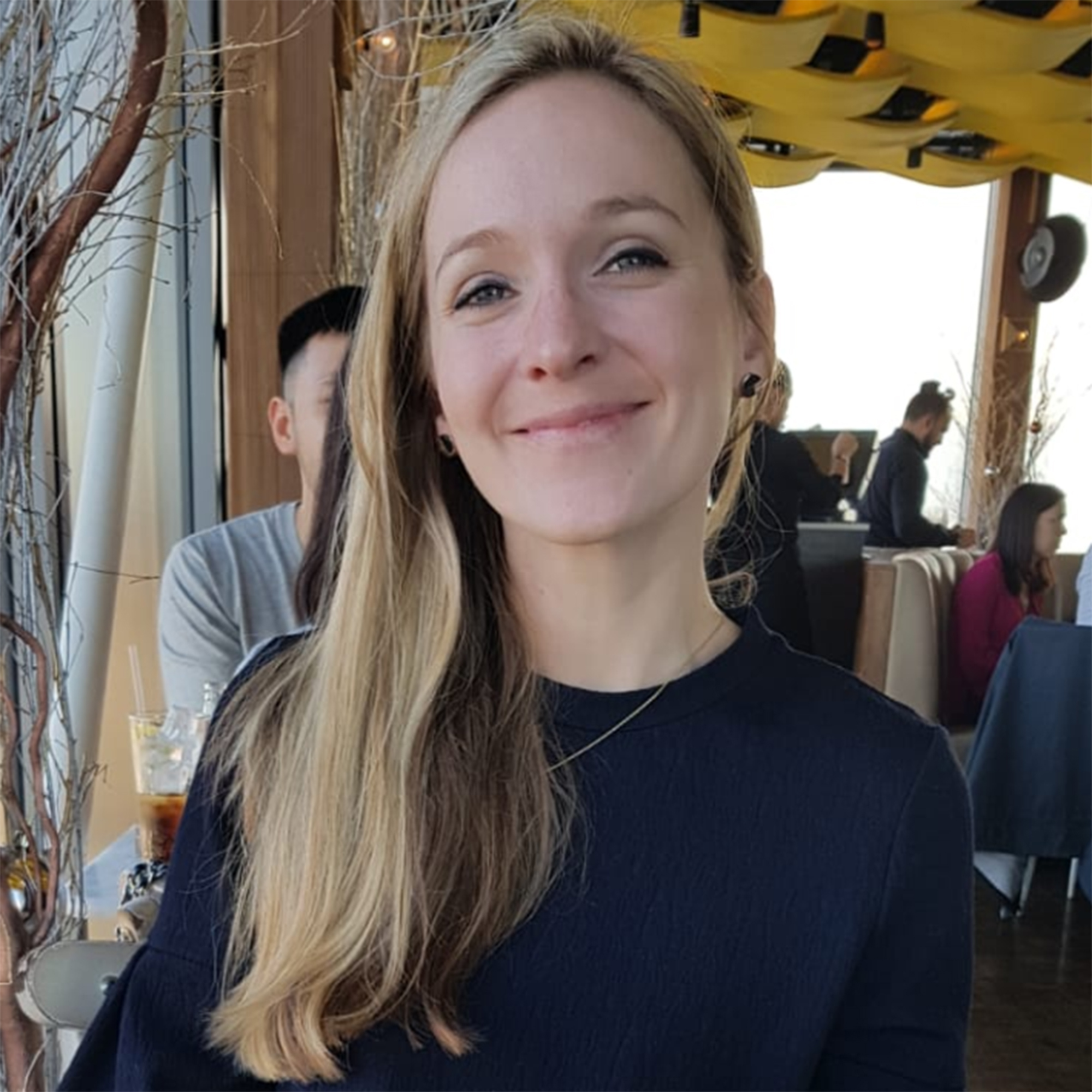
Rebecca Foster started her journalism career in Bangkok in 2013, where she worked on the in-house editorial team at a luxury homes magazine. Since then, Rebecca has contributed to numerous property and interiors titles in the UK and Southeast Asia. She re-located to London in 2015 to work at one of the country’s leading self-build and home renovation magazines. In 2017, she left her job to split her time between freelance journalism and teaching yoga.
-
Will a conservatory add value to your home and how can you maximise it?
This is what the pros say
By Amy Reeves
-
I’ve been looking for a new signature scent for my home and The White Company's new fragrance is the exact summer holiday smell I needed
Santorini smells fresh, summery and sophisticated
By Kezia Reynolds
-
How to remove algae from garden walls in five steps – and the cleaning product experts rave about for tackling it fast
Experts share their top tips for getting garden walls algae-free
By Katie Sims